This article provides the recommended steps for removing and installing the table slide cylinders.
If uneven movement or a chattering noise is occurring when the slide advances or retracts, the table slide cylinders will need to be replaced.
🗈 The lifespan of both cylinders should be approximately the same. For this reason, it is recommended to change both cylinders anytime one fails.
Ⓘ NOTICE Only qualified personnel familiar with the construction and operation of this equipment and the hazards involved should install, adjust, operate, and/or service this machine. Read and understand the manual in its entirety before proceeding. Failure to observe this precaution could result in severe bodily injury or loss of life. By proceeding, you are indicating that you acknowledge and agree that Foltex USA is not responsible for any damage to property or persons while accessing and/or using this service.
🔧 Tools you may need: ☐ Lockout, Tagout kit ☐ 3mm, 4mm, 5mm, 8mm hex keys ☐ 7mm, 13mm, 17mm combination wrench ☐ Adjustable spanner wrench (or channel locks) ☐ Medium to fine grit emery cloth ☐ Silicone spray lube
The steps below should be followed in order.
🗈 For reference purposes, the front of the machine will be considered the feed end of the machine, the rear will be the discharge end. Left and right will be observed facing the front of the feeder.
Remove the table slide cylinder
Ensure the stacker is in its lowest position before shutting down the machine.
Turn off the main disconnect located at the back of the unit and perform lock and tag procedures.
Locate and turn off the air supply to the machine and perform lock and tag procedures.
Remove the two front access panels using a 3mm hex key and the rear discharge conveyor panel using a 4mm hex key.
Remove the two air supply lines from the left and right-hand cylinders by releasing the quick connect coupler and pulling firmly on the air-line (Figure A, B).
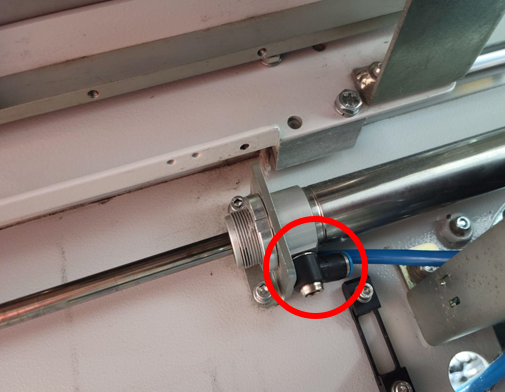
(Figure A) (Figure B)
Using an 8mm hex key, remove the 90° quick connect fittings from both ends of the cylinders.
Remove the shoulder bolts from both cylinder rod ends that secure the swivel joint to the slide using a 13mm combination wrench and a 5mm hex key (Figure C, D).

(Figure C) (Figure D)
Remove the encoder guard above the right-side slide cylinder by removing the four 7mm bolts.
Using an adjustable spanner wrench (or channel locks) remove both the front and rear spanner nuts.
Remove the front cylinder mounting brackets by removing the two 6mm hex bolts.
🗈 It is not necessary to remove the rear mounting brackets during this task.
Slide the cylinders backwards (towards the front of the machine).
Once the cylinders are out, remove the lock nut and swivel joint from the cylinder rods by using two 17mm combination wrenches.
Repair the table slide cylinder
🗈 It may be necessary to remove corrosion or wear from the swivel joint shoulder bolt.
Using fine grit emery cloth (320 grit or greater) clean the shank of the shoulder bolt until it is free of imperfections.
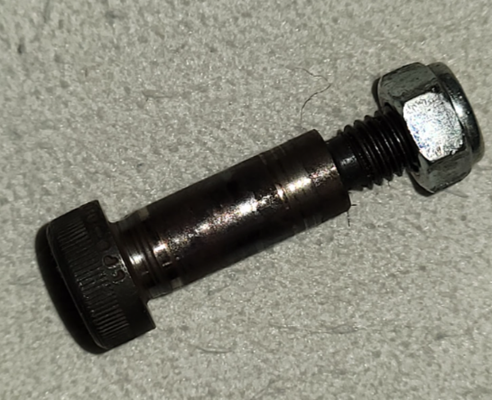
Spray the shoulder bolt and the swivel joint with silicone spray lubricant and ensure the joint moves freely.
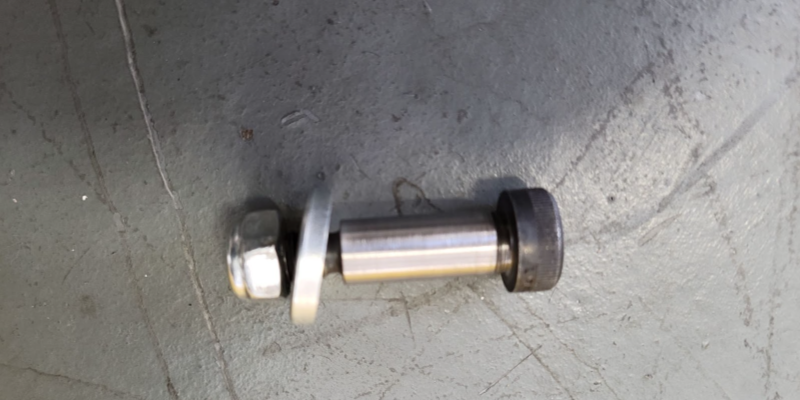
Install the table slide cylinder
Install the lock nuts and swivel joints on the end of the cylinder rods leaving approximately two threads showing on the rod. Do not tighten the lock nut or swivel joint at this time.
Slide the cylinder through the hole in the rear bracket mount and install the spanner nut. Do not tighten the spanner nut at this time.
Slide the front mounting bracket onto the threaded end of the cylinder and attach the bracket to the unit using the two 5mm hex bolts.
Install the front spanner nut onto the cylinder. Do not tighten the spanner nut at this time.
Reinstall the two 90° quick connect fittings on the new cylinders and reconnect the airlines.
🗈 The front airline is black and the rear airline is blue.
By hand, slide the table towards the rear of the machine. Adjust the swivel joint on the cylinder rod so it lines up with the hole in the bracket on the table and install the shoulder bolt.
🗈 When the swivel joint is adjusted properly, the shoulder bolt should drop in through the hole in the bracket and the swivel ball with little resistance.
Tighten the lock nut on the cylinder rod to secure the swivel joint.
With both cylinder rods attached to the slide table, move the table by hand to the front and rear of the machine several times ensuring there is no binding of the slide table.
Carefully tighten the spanner nuts on both cylinder mounting brackets (Figure E).
Ⓘ NOTICE It is likely the cylinder will shift slightly in the rear bracket while tightening the spanner nut. If this happens, there is a chance that the cylinder rods will bind when the slide table moves from front to back.
(Figure E)- Recheck movement of the slide table by hand to ensure there is no binding of the cylinder rods extending and retracting.
Remove any locks and tags you had previously installed and turn power/air back on.
On the touchscreen, go to the second page of the output menu (passcode required).
Press RESET FAULT ERROR 0 should appear on screen.
Press START TEACH for 5 seconds until button lights up slide will be in calibration mode until REF DONE light is on.
⚠ CAUTION Stay clear from the slide table during calibration as it may move unexpectedly.
Press Reset button and start machine.
Reinstall front and rear panels only after you have verified the machine is operating correctly.